The journey for any specific biosensor, in-vitro diagnostic or wearable biosensor is very individual, and is based on both technical and non-technical considerations, including: the target analyte, the form factor of the product, the target market, whether the correct funding is in place, and whether it is a regulated or unregulated application/market, etc.
On this page we discuss the technologies and workflows that Zimmer and Peacock has in place to accelerate the productization and commercialization of electrochemical biosensors, IVDs and wearable electrochemical biosensors.
You will note that in the ZP contract ISO13485 biosensor and IVD development and manufacture we don't focus on a single aspect of the sensing system , this is because we understand that all aspect of the sensing system have to work together and so we avoid the confusion of multiple vendors supplying a single aspect to the product development and confusing as to who is ultimately responsible for the system performance.
At ZP we understand the interaction between the electrode, the assay, the electronics, the fluidics and the quality system, and so the real value add from ZP is when we can work with your internal team to ensure that all aspects are tuned to work together.
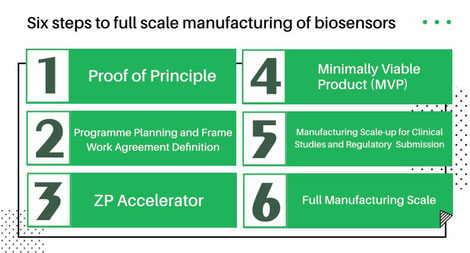
Managing an electrochemical biosensors and IVDs to market is a complex endeavour with a lot of interacting parts and it is ZP's Programme Management Group that ensures that we coordinate the complexity to deliver.
On this page ZP lays out at least six steps to go from idea/concept to full scale manufacturing.
- STEP ONE - Proof of Principle
- STEP TWO - Programme Planning and Frame Work Agreement Definition
- STEP THREE - ZP Accelerator
- STEP FOUR - Minimally Viable Product (MVP)
- STEP FIVE - Manufacturing Scale-up for Clinical Studies and Regulatory Submission
- STEP SIX - Full Manufacturing Scale
STEP ONE - Proof-of-Principle
In ZP's workflow the first questions are;
1) What is it you are trying to measure?
2) Does ZP have the sensor already, do you have a sensor, or does the sensor need to be developed?
Even if the sensors exists then they may have to be tested in a matrix that is more relevant to the final application, these include: saliva, breath, nasal swab, blood, sweat, tear film, interstitial fluid etc.
A good first step with ZP is a proof of principle study.
Zimmer and Peacock would aim to deliver to a Technology Readiness Level (TRL) 3 to 4, and Manufacturing Readiness Level (MRL) 4 to 5, but these are highly dependent on the specifics of the programme - read more.
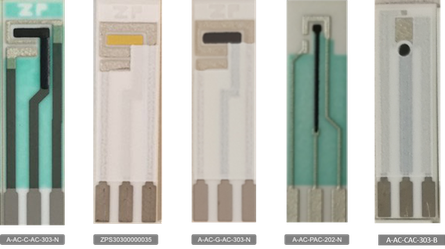
Part of the power of the Proof-of-Principle from ZP is our proprietary Cloud Data Djuli, click the button above.
STEP TWO - Programme Planning and Frame-Work- Agreement Defining
In STEP ONE we will have proven that the technology idea works in principle; in STEP TWO we are planning the programme and agreeing the Frame-Work-Agreement that will govern the relationship between ZP and the client.
The deliverables are at least a Gantt Chart, a presentation and if both parties agree a signed Frame-Work- Agreement.
It should be noted that the correct planning phase effort should take at least 50 to 100 hours. The timelines of the final plan are in part controlled by the total client budget and the rate of funding available. In order to plan then the ZP team will of course need input from the client.
STEP THREE - ZP Accelerator
The philosophy at ZP is to move technology out of the lab as soon as possible (ASAP). The ease of doing this is dependent on what ZP discovers and develops in STEP ONE, but important factors include: Limit-of-Detection (LoD), immunosensors versus enzyme sensors, IVDS versus wearable. The planning in STEP TWO is similarly important for this STEP THREE, as ZP will use outputs from STEP ONE and STEP TWO to calculate details like the effort to fabricate the sensors required in this STEP THREE.
The intention of STEP THREE (The ZP Accelerator) is to find out issue in the real world with real samples.
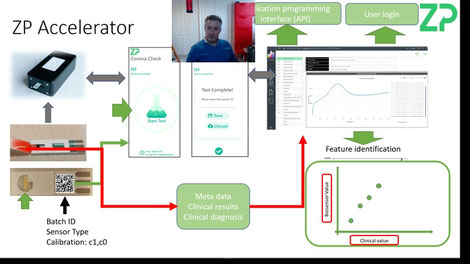
STEP FOUR - Minimally Viable Product (MVP)
Zimmer and Peacock is an ISO13485 contract developer and manufacturer of electrochemical biosensors and IVDs, which is relevant when discussing MVP.
In the software industry MVP is clearly a product with the minimum feature set that allows users/customer to start using the product. The concept of MVP can be applied into the biosensor and IVD applications, but extra consideration has to be put into the quality management system (QMS) around the product. The timelines and cost of the MVP are really dependent again on the technology, markets, regulatory landscape and most importantly the ability of the ZP collaborator to fund their product development programme.
The concept of MVP and iterative product improvement is distorted in the medical field, as changes in a medical product are very carefully controlled and changes can cause the need for the product to be re-submitted to regulatory bodies for expensive re-examination.
Zimmer and Peacock has detailed medical diagnostic programme plan templates based on effort on developing and manufacturing multiple electrochemical medical diagnostics.
STEP FIVE - Manufacturing Scale-up for Clinical Studies and Regulatory Submission
The first three steps are really just the start of the effort, once we have achieved STEP ONE, TWO, THREE and FOUR then the technology development for the first release of the product is mostly done, but now we are left with ensuring supply of high quality products for clinical studies so that there is sufficient data for supporting submissions to regulatory authorities, whether it is FDA, CE marking, 510(k) etc.
Zimmer and Peacock would aim to deliver to a Technology Readiness Level (TRL) 9 and Manufacturing Readiness Level (MRL) 7 to 9 but these are highly dependent on the specifics of the programme and most importantly the funding in place- read more.
STEP SIX - Full Manufacturing Scale
ZP is an ISO13485 contract developer and manufacturer of electrochemical biosensors and IVDs. As one completes regulatory submission or receives CE marking etc., and maybe enters into the second or third year of sales then it may be necessary to then ramp up to full scale manufacturing. At the time of writing this article ZP's largest facility is 4000 square meters and so is able to host most scales of manufacturing.
The intention here is MRL10 - read more.