ZP was approached by a research student with a question about their paper electrodes they had made in their academic labs; at the moment there is a lot of interest within the academic literature as paper microfluidics and paper biosensors are seen as a strategy for reducing the costs of biosensors and medical diagnostics.
At Zimmer and Peacock we screen-print, digitally print, sputter, etc to fabricate our electrodes on substrates ranging from ceramics, PET, Mylar, Kapton, glass etc, therefore we were happy to advise the student on their results.
The researcher was fabricating carbon electrodes on paper and was functionally testing their electrodes with 10 mM K3Fe(CN)6 containing KCl 100 mM, the researcher was concerned and thought that maybe their electrodes did not work.
The first thing ZP said was ‘…send us your data…’; we took a look at the data and confirmed that the electrodes were in fact working. The electrodes were not optimal and therefore the cyclic voltammograms were not classical and there was a variation between electrodes, but for ZP the electrodes were working, but just not as well as the researcher was expecting/hoping.
Whenever one is working on a sensors or a medical diagnostic it is worth asking what are you trying to achieve, are you:
- ONE - Performing a proof-of-principle to demonstrate that an idea works.
- TWO - Are you trying to prove that the electrodes are functional and superior or at least as good as a classical electrode material.
- THREE – Are you trying to achieve both TWO above and manufacture/fabricate these electrodes in a reproducible way.
In terms of difficulty ONE is the easiest to achieve, followed by TWO and with THREE being the most difficult to achieve. We often find that people are trying to achieve THREE but to fully achieve THREE then one needs to manufacture large batches of electrodes, and show that they can continue manufacturing electrodes with the same performance for several months, what we are in fact describing is a manufacturing line. On an manufacturing line the controls and procedures that are in place include:
- Raw material are tested, controlled and stored correctly.
- The manufacturing equipment is routinely calibrated and maintained and there are specific machines dedicated to specific products.
- The environment is controlled in terms of light, temperature, humidity and particulates.
- The is a quality control system measuring the inputs into the manufacturing system and measuring the output of the system, including functional testing of the electrodes.
- The process will have trained operators following standard operating procedures and keeping quality records.
The author would suggest that to achieve THREE above one needs to be following A to E. A good metric for how well one is manufacturing a sensor is the coefficient of variation (CV), it is worth being mindful of the electrochemical glucose sensors for testing diabetics whose CV values are 15 % to 20 %. To return to our researcher they were trying to achieve THREE, which was the hardest target, and because they were in an academic lab surrounded by undergrads, grads and post grads the control parameters were not necessarily in place.
If you have a question regarding electrochemistry, biosensors, medical diagnostics and how ZP's technologies can help please click the buttons below and feel free to contact us.
The student sent through the data and we were able to have a look, the 4 CVs shown are electrodes made at the same time and are tested with the same solution.
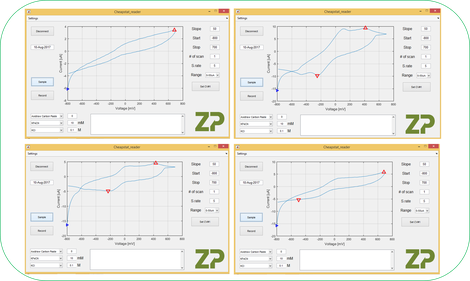
To help the student understand why their data was distorted we used an example of our sensors from the literature. We showed them a series of cyclic voltammograms (CVs) on a gold electrode of ferri/ferrocyanide. We discussed that the best CVs were on the bare gold but as we added more biochemical layers to the gold the CVs became more and more distorted as we were blocking the electrodes and increasing the resistance of the electrode (increasing the charge transfer resistance Rct). As a side comment it is absolutely not necessary to have an electrode producing beautiful electrochemistry data in order to have an electrode applicable to the market place.
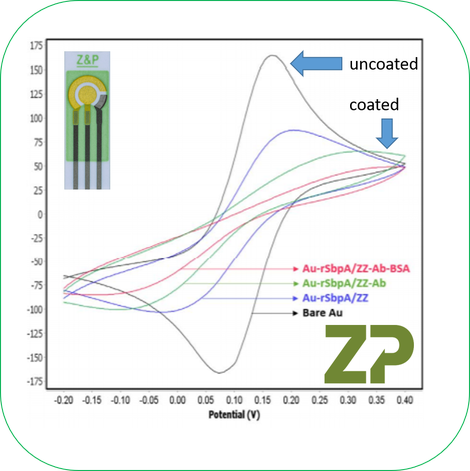
When you do a side-by-side comparison between the student’s data and data from a coated ZP sensor you would argue that they were both distorted and we advised the student that the distortion was due in their case due to poor conductivity of the ink.
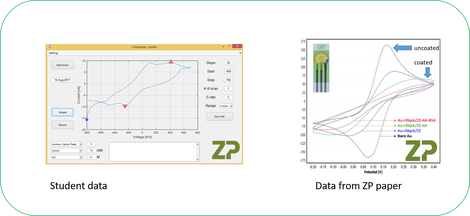
We sketched out a line, which was compelling as it went through the origin and argued that in their data there was an high resistance (possibly/probably the ink) and this resistive element was distorting their data in line with Ohms Law.
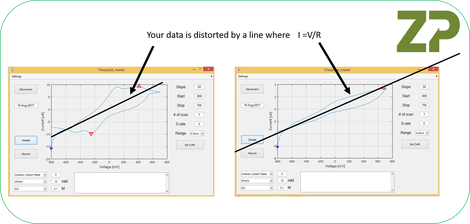
Next we asked the student to do was to run some amperometric experiments as we wanted to illustrate the point that your electrodes don’t have to give classical cyclic voltammograms to be a good sensor ;our instructions were ‘…hold a single electrode in an amperometric experiment at -300 mV vs RE and test the same 1, 2, 5 and 10 mM K3Fe(CN)6 again in 100 mM KCl..’ We drew a sketch of what we were expecting.
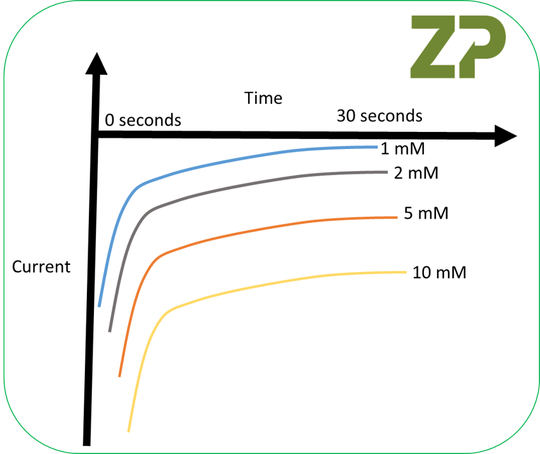
The student did as requested and the results were very close to what ZP had predicted.
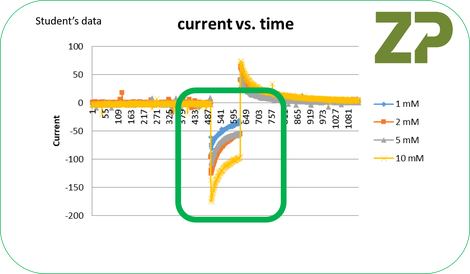
The predicted data and actual data were similar, in the actual data the 2 mM and 5 mM showed similar responses and could be accounted for by a drift in the electrodes with repeated use or a variable in the experimental set-up. In addition the scientist measured the resistance of their electrodes and found they had several kOhms of resistance . Lastly they found that the electrodes’ had resistance that varied by 15 to 20 % across their batch.
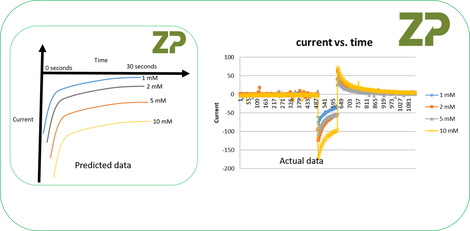
We finished the free consultation to the student by writing a summary which was ' ..we have designed a paper electrochemical sensor where the electrodes were printed using a conductive carbon ink. We have characterized these electrodes using cyclic voltammetry and amperometry.
- By cyclic voltammetry – it was clear that the CVs were not classical for a reversible electron transfer when we characterized the electrodes using 10 mM K3Fe(CN)6; rather the CVs were distorted, and behaved somewhat like a electrochemical system in series with a large ohmic resistor, it was therefore concluded that the electrodes had quite high impedance, which most probably reflected the print thickness and the organic binders used to create the ink. When tested with a voltmeter we discovered that the electrodes indeed had kilo-ohm resistance.
- By amperometry – many commercial sensors and biosensors in fact do not operate by cyclic voltammetry but rather by amperometry, e.g. the majority of glucose sensors on the market operate using amperometry and therefore we wanted to test whether we could gather meaningful results when testing by amperometry, therefore we again tested using K3Fe(CN)6 but at four concentrations: 1, 2, 5 and 10. Our hypothesis was that it was more meaningful to test our electrodes using the analytical method most likely to be used in a real-world commercial environment. We found that the sensors could clearly separate a 1mM solution from a 10 mM solution, whilst could not separate 2 from 5. We could therefore conclude that we have functional paper based electrodes, but we would have to further optimize if we want greater assay resolution. We have noted that for some assays it is important to have a sensors able to resolve concentrations, i.e. home diabetes monitoring, whilst for other assays such as hCG detection for pregnancy testing only requires a YES or NO answer, so we can conclude that the electrodes are good enough for assays where YES or NO was appropriate whilst for other applications the electrodes would have to be improved to increase the assay resolution.
Our electrodes are made using a workflow which consists of: making the inks, printing the inks and curing the inks. Each step can be a source of variation and we know that these sources of variation accumulate to give us a 15 to 20 % variability in electrical resistance of our electrodes across a manufactured batch of electrodes. We also understand that it’s only through high volume commercial manufacturing that electrode variability can be drive down