Zimmer and Peacock is focused on helping our clients and partners get to marker ASAP with electrochemical sensors suitable for field applications.
For a screen printed electrode to be commercially successful in the field the following FEATURES are important.
1. FEATURE ONE - The sensor must have the potential to be low cost, so to ensure the highest margins.
2. FEATURE TWO - The sensors have to function correctly.
3. FEATURE THREE -The sensors should operate at a low power, with simpler electronics.
It is with these FEATURES in mind that ZP has started to promote the ‘value range’ over our first generation of sensors and electrodes.
In the following sections we discuss why the ZP ‘value’ sensors are superior over the ZP first generation of electrodes.
FEATURE ONE - COST
The ‘value’ sensors are 44 % smaller than the generation one sensors. This means that when manufacturing sensors in processes such as sputtering, flat-bed screen printing, roll-to-roll printing etc one will produce 1.8 times more value sensors for every one ZP sensors. Clearly the production capacity can be approximately doubled by this simple change with little or no CAPEX expenditure.
ZP also sees the ZP value sensor’s benefits translating into other downfield processes, for example if sensors are functionalized by a digital printing process it is possible to functionalize a sheet of value electrodes and produce 1.8 more sensors before having to do a card/sheet change.
The smaller form factor adds benefits further downstream when it comes to packing, storing and shipping.
ZP does understand that you cannot make a sensor so small that the user can no longer handle the sensors, and so we have surveyed the glucose strip market before coming to the final decision on the value sensor size; we also now have practical experience from our ChilliPot product which is on the market and uses the value sensor form factor.
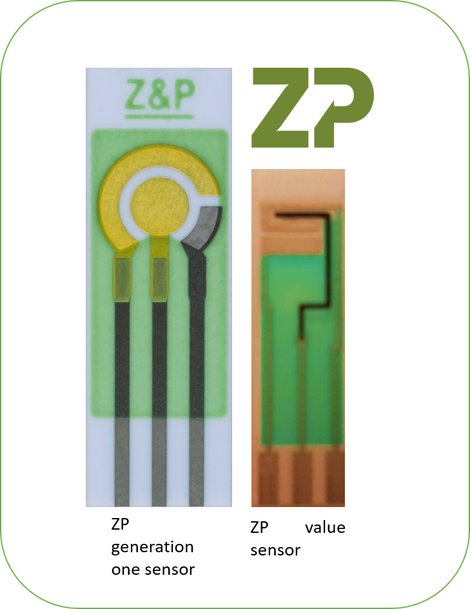
FEATURE TWO – CORRECT FUNCTION
ZP employs a number of principles from the glucose strip market and so it is fairly achievable to make microfluidic/capillary fill sensors with electrodes in close proximity to one another and where the sample volumes can be below 1 microliter.
Whilst it is both a nice feature for the clients to have the ability to use sample volumes as small as 300 nL it does introduce an issue not commonly considered by electrochemists, which is ‘what is happening at the counter electrode?’
In traditional electrochemical thinking what happens at the counter electrode has been mostly ignored based on the following assumptions:
1) ASSUMPTION ONE - The counter electrode has been traditionally large relative to the working electrode.
2) ASSUMPTION TWO - The counter electrode has traditionally been at some distance from the working electrode.
3) ASSUMPTION THREE – Traditionally the solution within the electrochemical cell has been large relative to the electrodes.
The three assumption above are used by electrochemists to say that the counter electrode is not so important when understanding the signals within an electrochemical sensor, but these assumptions are not necessarily valid in very small volumes associated with electrochemical sensors and biosensors which have capillary/microfluidic chambers upon them.
Let’s consider a thought experiment containing an electrochemical assay which operates by applying 650 mV to the working electrode; in this assay the analyte is oxidized at the working electrode, at the counter electrode an equimolar reduction reaction is occurring in parallel with the working electrode reaction. The reaction at the counter electrode is often not known or fully characterized and can be influenced by a number of parameters including: the concentration of oxygen, the pH, the current driven at the working electrode.
Therefore, there are at least three variables that govern what maybe happening at the counter electrode, one thing one can often be certain of when using a traditional carbon platinum or gold electrode which is that the counter electrode electrochemical reaction is at best unclear and often unknown.
The issue is that the unknown products at the counter electrode may diffuse across to the working electrode and so after some seconds the products of reaction at the counter electrode may start to influence the reactions at the working electrode and therefore introduce an otherwise over-looked and uncontrolled contribution to the signal effect, this is schematically.
The diffusion of material from the counter electrode to the working electrode in systems where the electrode spacing is millimeters can happen on the seconds to 10s of seconds time range, and so this event can influence the signal. The observable effects of this diffusion can be numerous, but one possible outcome is an electrochemical feedback loop where the reduction product at the counter electrode diffuses to the working electrode and is subsequently re-oxidized. This re-oxidation in turn causes a further increase in current at the counter electrode which in turn drives further diffusion of reduced material from the counter electrode to the working electrode hence further driving up the current, this is in effect a closed loop electrochemical feedback system , we illustrate such a scenario in the adjacent figure.
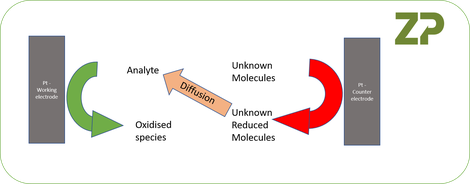
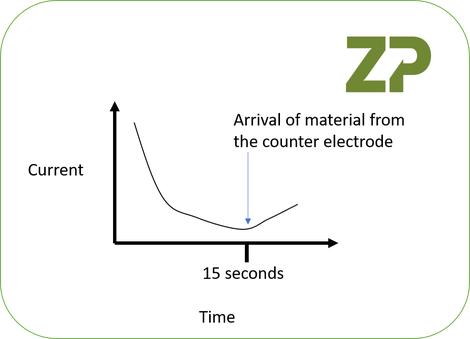
At Zimmer and Peacock we have observed the phenomena described in the figure, and have had it reported to us by others in the glucose strip market.
With the ZP value sensors we have eliminated this effect by instead of having just a bare carbon, platinum or gold counter electrode we instead have a silver/silver chloride counter electrode. What this means is that if the counter electrode is at a negative voltage then the silver chloride is reduced to silver which is an insoluble product and therefore will not diffuse to the working electrode; of course the counter to this is if the counter electrode is a positive voltage then the silver is converted to the insoluble silver chloride which again does not diffuse to the working electrode.
The use of silver/silver chloride on the counter electrode of the ZP value sensor at the very least produces a defined reaction on the counter electrode which would otherwise be an unknown reaction which can have unexpected outcomes.
Feature 3 – Power
Though not a topic often discussed the power it takes to drive an electrochemical sensors and biosensors can be linked to two parameters:
1) The working voltage – the voltage applied to the working electrode relative the reference electrode.
2) The compliance voltage – the voltage applied to the counter electrode to ensure that the reaction at the counter electrode is not the rate limiting step to the reaction at the working electrode.
It is often overlooked by sensors designers that the chemistry at the counter electrode can influence the power consumption of the analog electronics; for example, if no particular care is taken on the counter electrode material then the compliance voltage maybe - 0.9 V due to the reduction of water. Therefore if the voltage on the working electrode is 0.25 V, the entire cell potential is 1.15 V. A simple change of material on the counter electrode to silver/silver chloride means that there is now the potential for a very facile reaction on the counter electrode as silver chloride can be converted into silver, and similarly silver into silver chloride in the case of a positive voltage at the counter electrode. The conversion of silver and silver chloride occurs at a compliance potential close to 0 V and so the cell potential for a sensor where 0.25 V is applied the working electrode will now be approximately 0.25 V, as opposed to the previous 1.15 V. This can result in both simpler electronics running at a lower power duty.
SUMMARY
Zimmer and Peacock is promoting it’s value sensors over the more traditional sensors because we see that it offers several commercial and technical advantages over the more traditional sensor form factor.