Why are sputtered electrodes and screen-printed electrodes so variable?
THE PROBLEM
At Zimmer and Peacock we supply screen-printed electrodes, sputtered and ablated electrodes and a hybrid electrodes, where we mix manufacturing techniques. One of the most common complaints we hear regarding electrodes manufactured by others is that the electrodes are too variable both within an electrode batch and between electrode batches.
Zimmer and Peacock are fairly unique in the world of electrochemical sensors and biosensors in that our focus is partly on the R and D of these sensors, but really our focus is on making sensors in high reproducible volumes and getting our collaborators through clinical trials and to market.
One of the questions we will answer in this note is ‘why when I buy a batch of screen-printed or sputtered electrodes they are different when I buy the same electrodes 6-months later.’ We appreciate that the reason for this is evident to some but let us list some reasons below:
REASON ONE – The electrodes are possibly from different batches. Though the manufacturer is trying to make a reproducible product they are in reality not achieving this. The reason is a volume one, what we mean by this is they are actually making quite small numbers of electrodes maybe 500 to 2000 or 20,000 sensors/electrodes depending on their facility and fabrication technique; when they finish the manufacturing run they clean the machine down and the next day they are making a slightly different product. Then 6-months later they decide to make a second run of products but the person, the machine set up, the raw materials, the ambient conditions are not an exact replication of the previous run and the electrodes that are now produced have different properties to the original batch of electrodes.
REASON TWO –The second reason for irreproducibility is just the standard operating procedures within the fabricating facility are not in place or are not well adhered to so the recipe for how to make an electrode is not written down or followed properly.
REASON THREE- Very few contract manufacturers of electrodes for the R and D market are able to perform large numbers of functional testing of the electrodes. A visual inspection or contact angle test is often performed, but unfortunately this is not indicative of electrochemical functionality. The issue is of course that electrochemistry has many AC and DC techniques so it is difficult for a manufacture to test for and guarantee repeatable performance across the range of electrochemical techniques.
THE SOLUTION
What is the ZP solution?
At Zimmer and Peacock we are pragmatic industrial bioelectrochemists, which means we understand that electrodes made for the R and D market though may look consistent, but they will in fact not have the within and between batch reproducibility required for electrodes and sensors that are intended for real-world applications. What ZP does that is different is when we are on a programme that is truly aimed at getting customers to market we functionally test large samples of electrodes from a batch in a manner that its appropriate to the final application. We demonstrate this below., where we have functionally tested a high number of sensors from a batch of sensors (electrode with biologically active component printed on top), and performed statistical analysis on the batch so we can understand the variability within the batch.
Our pass criteria is not are the sensors perfect, but rather are they good enough for the real-world application. In this case, can the sensors separate sick patients from healthy controls.
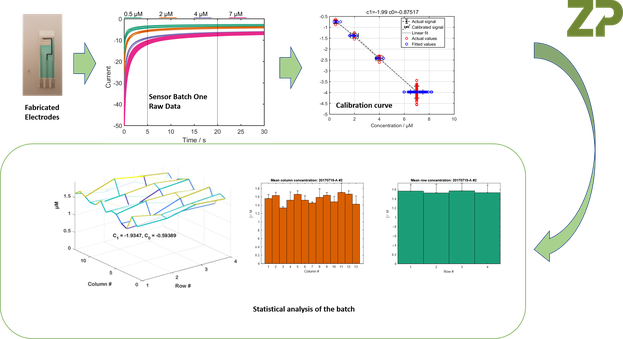
The Figures above constitute a wafer mapping procedure.
The analysis of the electrodes was a functional test so we have sacrificed 10 % of the batch of electrodes/sensors in order to perform the study.
The issue with the screen-printed electrodes/sputtered electrodes is that you can have a number of surrogate tests such as visual inspection, contact angle measurement etc, but the only test that will really tell you how your sensors/electrodes will perform in the field is a functional test.
When manufacturing sensors, biosensors, screen-printed electrodes and sputtered electrodes it is not enough to characterize one batch of electrodes; the characterization has to be repeated every time a batch of electrodes are made. The issue at the heart of anyone making biochips is that batch calibration has to take place every time and not on one or two electrodes but typically multiple tens to hundreds of sensors.
In the images below ZP is showing the data from two further batches of sensors, it is important to know that there are several man days of effort to gather and analyse this data and is partly why sensors/scree-printed electrodes/sputtered electrodes have a high cost when intended for critical applications such as medical diagnostics.
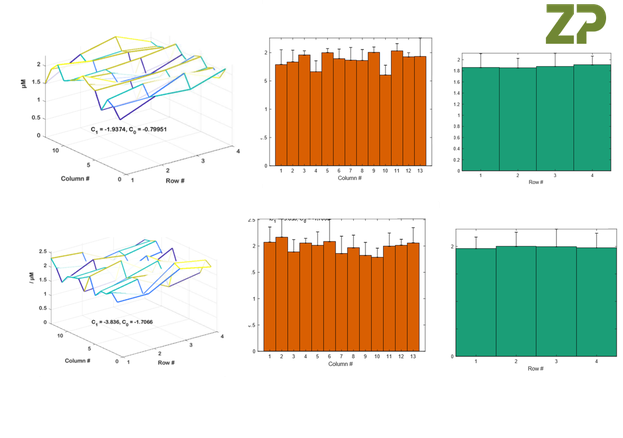
The Figures above constitute a wafer mapping procedure.
The reality of making screen-printed electrodes, sputtered electrodes, and sensors is that they are not necessarily functionally tested or tested in high enough numbers to have really characterized the batch of sensors/electrodes. ZP is unique in that we have the capability of making high volumes of screen-printed/sputtered electrodes and to functionally test them to ensure them in the final application. ZP offers two levels of products:
1) Standard Research Products and Service – these are products and servie sufficient to get to proof-of-principle.
2) Manufacturing for clinical trials and on market products - here we put in several man days to test the electrodes/sensors to ensure overall bath performance, and between batch performance.